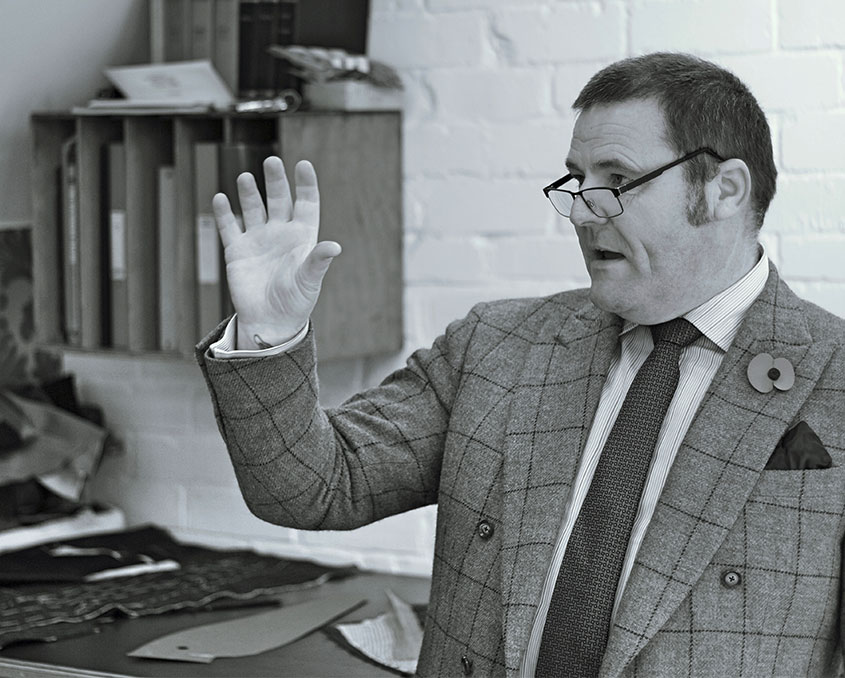
The Beginning
My late Father Terry wasn’t a tailor, he was an engineer, a sewing machine engineer, and a really good one. He eventually became the chief engineer for the world’s largest merchant tailor, Montague Burtons’. This is how I really got started onto the tailoring path. My earliest tailoring recollections are as a young boy aged about 6 running into the vast Burtons’ Hudson Road tailoring factory in Leeds on a Saturday morning with my father. The picture above was taken in the cutting room of Montague Burton’s Leeds Hudson Road factory 1967.
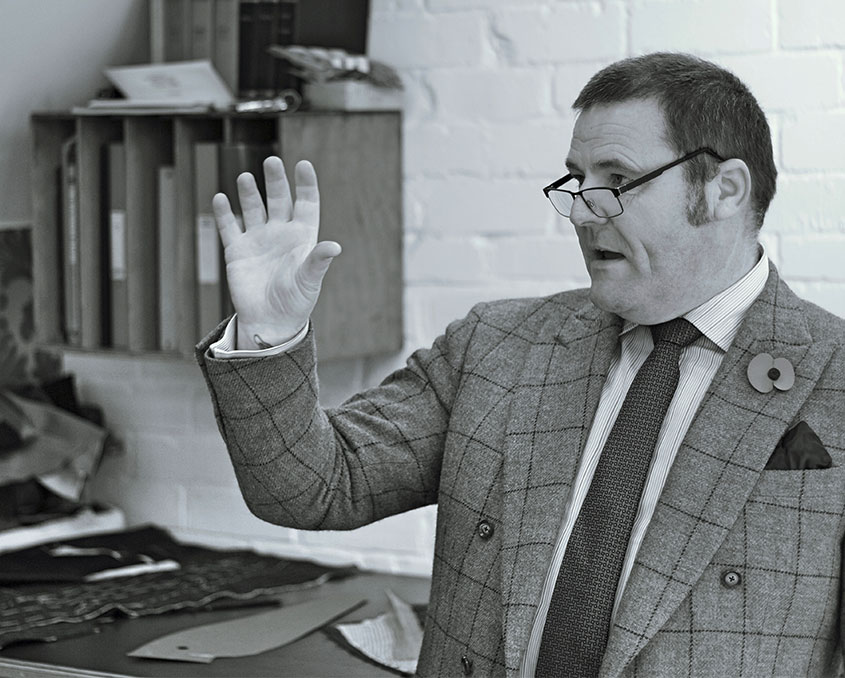
Sir Montague Burton
At the weekend my father would sometimes have to go into work and would often take me with him to the Burtons’ factory that was on Hudson Road in Leeds. But not only the Leeds factory, he would also have to go the other Burton’s factories which were located at Doncaster, Goole and Guisborough that he was also responsible for overseeing. But, it’s the Leeds factory that has always stayed within my memory, purely down to its sheer size, tailoring on an immense scale that will never, ever be seen again. To this day, almost fifty years later, I can still see the rows upon rows of men and women sat hand sewing the suits Burtons’ made…
Keep reading
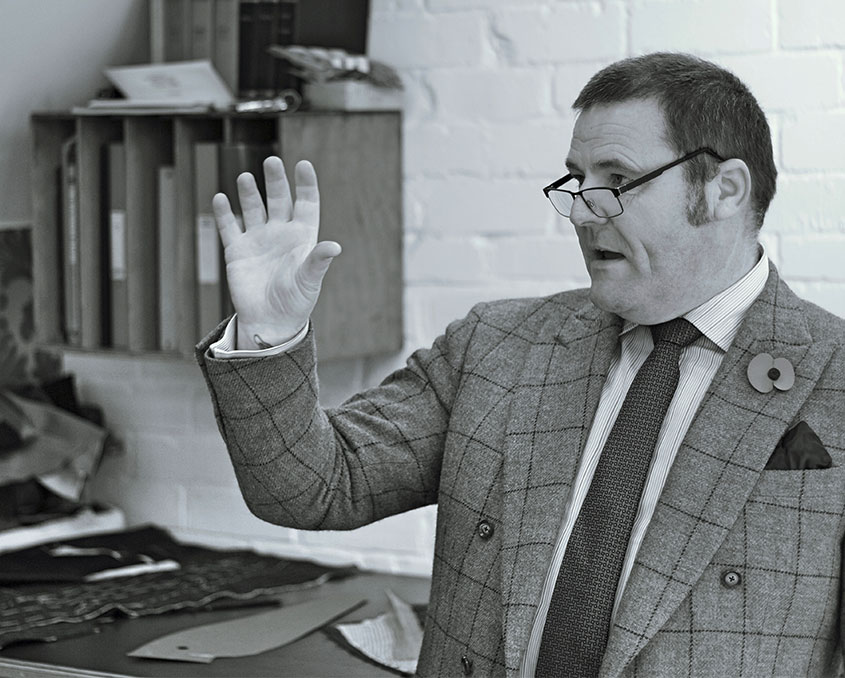
Menial Tasks
I had always, always wanted to join The Army, I was army barmy from around three years old, becoming an Army Cadet just before I was 13 years old. I was absolutely set upon becoming a gunsmith and I was always intending to join the Royal Army Ordnance Corps as an armourer as a start onto the gunsmithing path. Ironically this had been my fathers regiment during his two years national service 1958 to 1960.
Keep reading
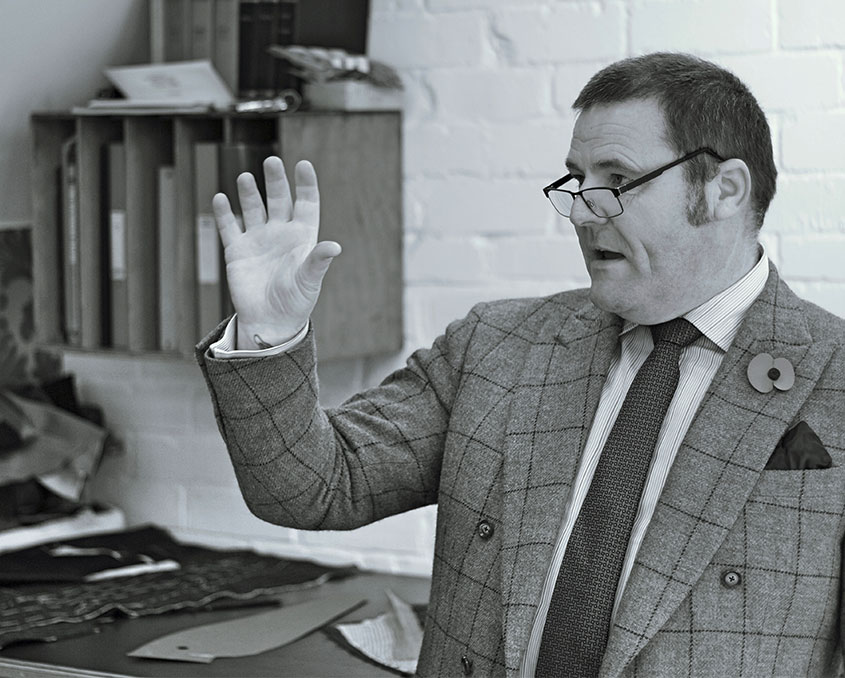
Extra Tuition
Right place, right time, it had all happened very quickly for the three relatively new business partners. It was sometime around the summer of 1986 and the factory was booming, absolutely stuffed to the rafters with more work than it could handle. The factory had also grown very quickly from a starting size of 50 hand picked workers in the first year, to 100 workers in the third year, all initially housed within a 5,000 sq ft factory that would eventually peak at 220 workers spread over an open plan 25,000 sq ft work floor. But, like most things in life it wasn’t all plain sailing, Eddie had cancer and he would barely live to see the year out, It all happened so fast, in a blink. Buying the unit either side, knocking the adjoining walls out, expanding the factory, the never ending overtime, Eddie’s death. It was a whirlwind and it seemed like it would never end.
Keep reading
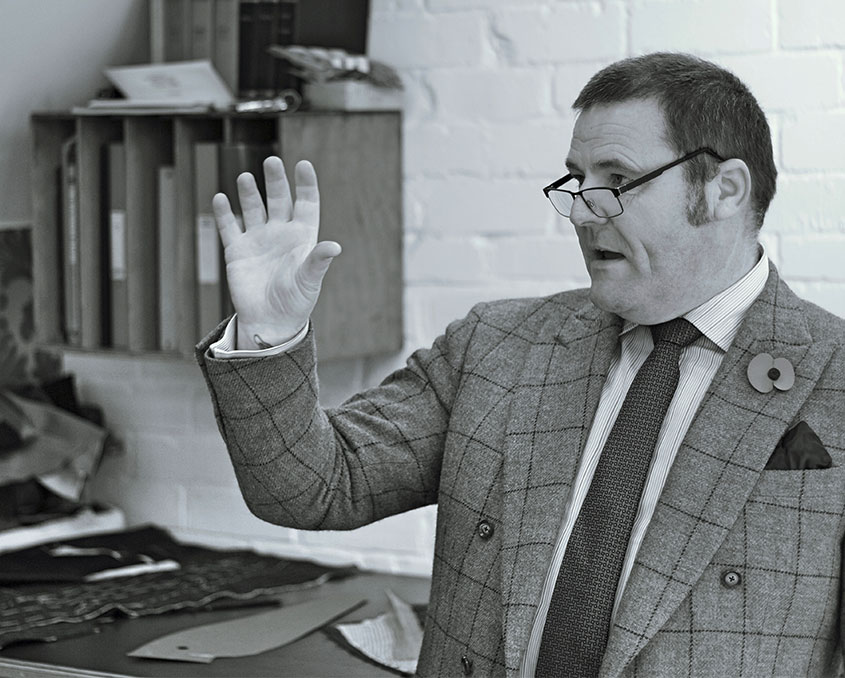
A King Cutter
After a long time training and learning, I was eventually let loose on cutting the various trimmings required for trousers and jackets, trimmings are the small ancillary parts required to make the garments.
My next step was to mark in the garments for the other cutters prior to them cutting them out. I had been with the company for a few years by this time and my wage had increased from £30 per week to £1.67 per hour. As a comparison my friends working in the construction trades earned more bonuses on top of their salaries than my entire take home month’s wage.
Keep reading
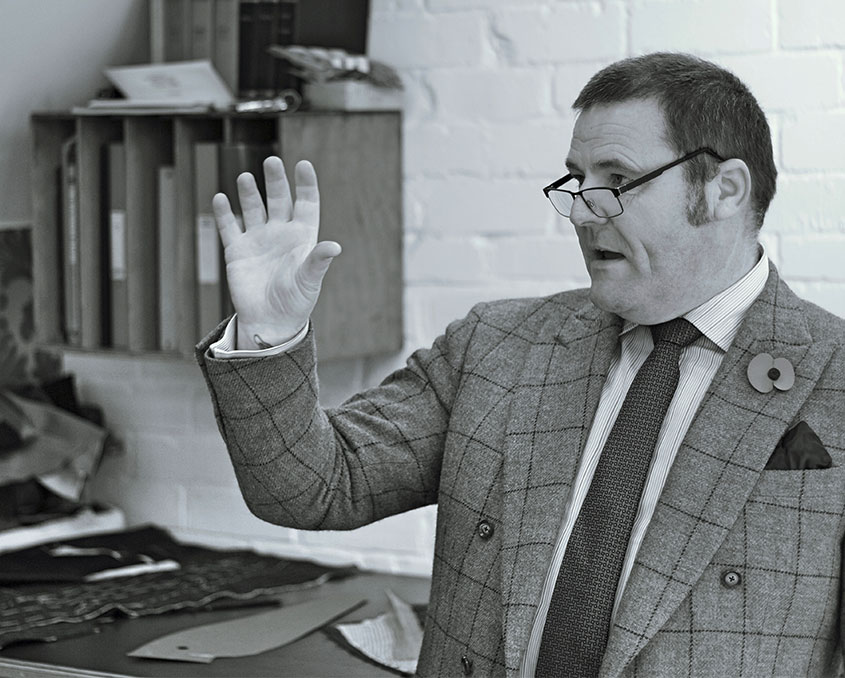
The Art of Pressing
The factory was CMT (cut make and trim) so the range of different styles we made was immense. We didn’t actually make that many garments under our own label, we were primarily here for others that required a manufacturing facility. There was always what we’d consider the normal production run of suits, bread and butter stuff, single breasted, straight pockets etc, but as a specialist factory we also catered for everything from shooting garments with bellows patch pockets and ‘action’ pleats in the back, through to high end ridiculously styled designer garments. I was fortunate to be able to see, and learn a real skill that few possess today, how to press jackets off by hand. Even though the factory was full of what was at the time quite high end semi automated pressing equipment, Betty Turnbull and Janice Butler, along with other names that sadly I can’t remember, would still be pressing by hand.
Pressing is an art, a touch that can’t be explained, you feel the cloths requirements and they are all different. To say a good presser can make an average garment look outstanding is an understatement.
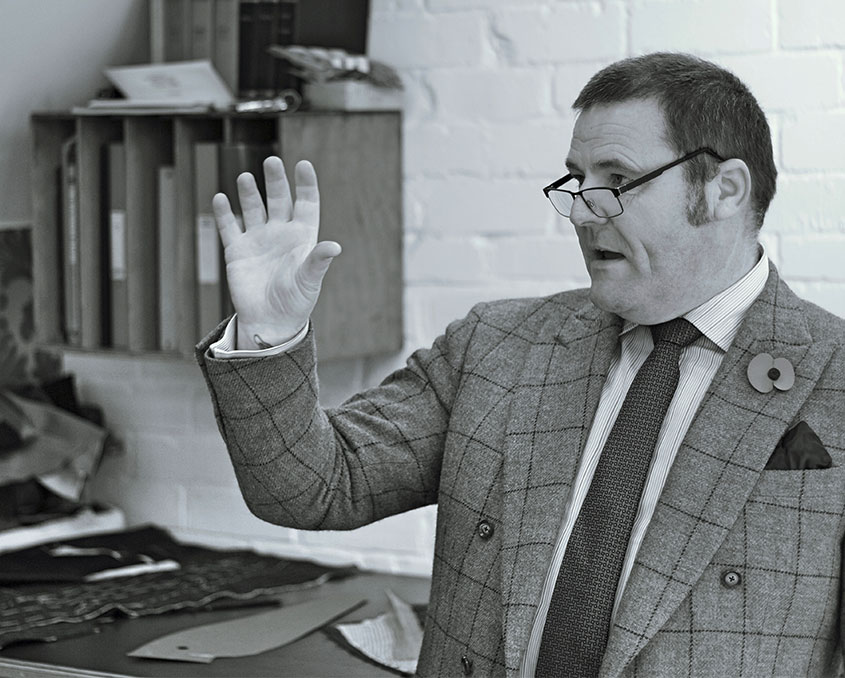
Friday Fun
The normal factory working week without overtime was 7.30am – 5.30pm. Monday to Thursday. I was approached by a friend of my father’s who asked if I’d be interested to cut garments out for him. So, every Friday I used to go and cut out for Brian. I didn’t really have much choice, I had to, my Father didn’t pay high wages. Brian had his own business, it was a right old upside down hole, stuff all over the place. Brian’s business primarily made country-wear, country-wear, for shooting and game keepers. I really enjoyed cutting out shooting suits and breeks in the most amazing colours and patterns in the John G Hardy tweed he used.
Keep reading
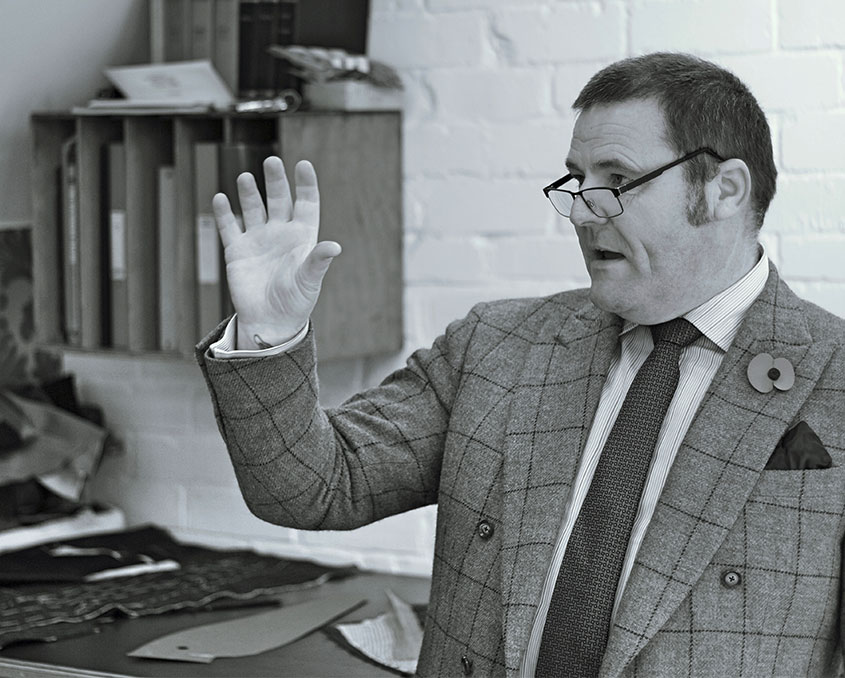
Going It Alone
The decision to wind the factory up came in 1996. My father and Janet, as they did every year, went down to London to see the buyers and discuss the coming years order book. On the horizon, the growing number of foreign factories undercutting UK prices was already making the margins very tight. My father told me they were offered work that would fill the coming year, but the garments would have to be made at the previous years prices. Dad and Janet asked if they could have a chat together, which they did, and they both agreed that they’d had a good run, done well and didn’t need to take the work. It was a very sad day but totally correct from a financial and personal stand point for dad and Janet. Janet’s older sister (who had been living in Australia for years) had been missing for a few weeks, and had subsequently been found dead in her car after a crash in the outback, Janet would have to go to Australia to make the funeral arrangements and could be gone for months. The building was owned outright by the company, along with all the plant and machinery in it and this was a considerable amount. I stayed with my father’s company right up to the point until my father and Janet sold up. My last job was to help dismantle the factory and strip it out. It was like watching locust.
Keep reading